2017.10.15
国际青年创客马拉松比赛是一项鼓励大学生创新创业的国家化赛事,小强用户因为小强的强大运算性能和教程案例,购买我司的小强机器人开发平台,通过不懈的努力,实现了小强机器人场景化,应用到创新实践当中去,取得了良好的效果,收到了评审老师的一致好评,最终取得了本赛事的一等奖,小强作为助攻功不可没,小强致力于在您的科研道路上助您一臂之力,和您一同成长,您可以让小强成为你心目中的完美伙伴,这取决于您的创意!
ROS Group 产品服务
Product Service 开源代码库
Github 官网
Official website 技术交流
Technological exchanges 激光雷达
LIDAR ROS教程
ROS Tourials 深度学习
Deep Learning 机器视觉
Computer Vision
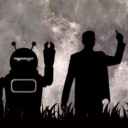
Yangoogle 发布的帖子
-
小强用户用取得国际创客比赛一等奖!
-
Xiaoqiang users won the first prize in the International Makers Competition!
2017.10.15
The International Youth Makeup Marathon is a nationalized event that encourages college students to innovate and start a business. Xiaoqiang users have purchased our Xiaoqiang robot development platform because of Qiangqiang’s powerful computing performance and tutorial cases, and through the unremitting efforts, realized the scene of Xiaoqiang robot. Applying to the practice of innovation, it has achieved good results. It has received unanimous praise from the judges and finally won the first prize of this competition. Xiaoqiang is a helper. Xiaoqiang is committed to helping you on your research path. With one strength, grow with you, you can make Xiaoqiang the perfect partner in your mind, depending on your creativity!
-
伽利略视觉导航系统成功应用在叉车定位场景
2017.10.07
蓝鲸智能机器人的伽利略视觉导航系统成功应用在东莞某企业的仓库中,伽利略视觉导航系统能通过单个摄像头获得在工厂中的叉车的实时定位,定位信息汇总到改公司工厂的ERP系统里面用作统计和整体调度,这个应用标志着蓝鲸的伽利略视觉导航系统正式进军工业物流领域,并且取得了成功。
本场景所在工厂仓库总共6个车间,万余平米,叉车加装伽利略视觉导航系统后可以获得实时定位,并且在地图中显示所在位置,并且定位系统并没有要求叉车自身有里程计等信息的上传,完全控制上独立于叉车的系统,这样系统的独立性方便了系统的加装和对接,简化了应用流程,降低了硬件门槛。 -
Galileo visual navigation system successfully applied to forklift positioning scene
2017.10.07
The Galileo visual navigation system of the Blue Whale Intelligent Robot is successfully applied in the warehouse of a certain enterprise in Dongguan. The Galileo visual navigation system can obtain the real-time positioning of the forklift in the factory through a single camera. The positioning information is summarized and used in the ERP system of the company’s factory. Statistics and overall scheduling, this application marks the official entry of the Blue Whale Galileo visual navigation system into the field of industrial logistics, and has achieved success.
The factory warehouse in this scene has a total of 6 workshops, more than 10,000 square meters. After the forklift is equipped with the Galileo visual navigation system, real-time positioning can be obtained, and the location is displayed on the map, and the positioning system does not require the forklift to have the odometer and other information uploaded. Full control of the system independent of the forklift, so the independence of the system facilitates the installation and docking of the system, simplifying the application process and reducing the hardware threshold. -
The visual positioning solution is finally complete
2016.3.28
The visual positioning solution is finally complete
Visual positioning and navigation algorithms are the focus of current robot research, and they are also the hotspots that everyone is studying. In actual use scenarios, the need for visual positioning is also large. However, there has been no mature visual positioning navigation solution in China. Today we finally succeeded in realizing a solution for visual positioning.Below is a video of our test comparing the visual positioning algorithm with the general method of using the gyroscope inertial positioning.
The test environment is Xiaoqiang (http://www.bwbot.org/zh-cn/content/xiaoqiang), a comprehensive development platform for ROS we developed. We use remote control to let Xiaoqiang repeat a square track with a length of about 1mX2m on the ground. Xiaoqiang also returns the coordinates calculated by the two groups according to Xiaoqiang’s gyroscope and camera. The above video is the position coordinates of Xiaoqiang displayed in real time on the computer. The red line represents the coordinates determined by the visual positioning algorithm, and the green line represents the small strong position coordinates determined from the gyroscope and motor encoder data. It can be seen that the results obtained by the first two methods are basically the same. As the number of turns around the gyroscope increases, the error of the gyroscope increases, but the coordinates calculated by the visual positioning do not change. This is also the advantage of a visual positioning algorithm.
Many of today’s restaurant delivery robots still use electromagnetic or mechanical rails to position the robot. Such an approach not only has a large cost to be retrofitted, but also has a high maintenance cost, and has a great influence on the overall decoration of the restaurant. With the visual positioning algorithm, no rails are needed to aid positioning. The robot has an eye that can really be used. The same industrial AGV robot can also provide more precise coordinates to the robot by means of visual positioning.
Update:
After a long period of test development, we have developed a stable and complete visual navigation system. That is, the Galileo visual navigation system. More detailed information can be found here (http://www.bwbot.org/zh-hans/content/galileo).Introduction to Galileo system documentation (https://galileo-servicebot-doc.bwbot.org/)
The Galileo Vision Navigation System is a robotic positioning and motion control system that incorporates multiple sensors and is guided by visual navigation. The positioning and navigation functions of the robot can be realized by loading the system. It is suitable for various application scenarios such as automatic inspection robot industry AGV, service robot and so on.
Below is an action video that includes creating a map and saving the map. More details can be found on the Galileo system related pages.
-
视觉定位解决方案终于完成了
2016.3.28
视觉定位解决方案终于完成了
视觉定位和导航算法是目前机器人研究的重点,也是大家都在研究的热点。在实际的各种使用场景中,对于视觉定位的需求也很大。但是国内一直没有比较成熟的视觉定位导航解决方案。今天我们终于成功实现了视觉定位的解决方案。下面是我们测试比较视觉定位算法和一般的利用陀螺仪惯性定位的方法的视频。
测试环境是我们开发的ROS综合开发平台小强(http://www.bwbot.org/zh-cn/content/xiaoqiang)。我们利用远程遥控,让小强在地面上重复的绕一个边长大概1mX2m的方形轨迹。小强同时返回两组分别根据小强的陀螺仪和摄像头计算出的坐标。以上视频就是电脑上实时显示的小强的位置坐标。其中红色的线代表根据视觉定位算法定出的坐标,绿色的线代表根据陀螺仪和电机编码器数据定出的小强的位置坐标。可以看出最初两种方法得到的结果基本一致。随着绕的圈数的增加,陀螺仪的误差越来越大,但是视觉定位计算出的坐标没有什么变化。这也是视觉定位算法的优势。
现在的餐厅送餐机器人很多还在采用电磁或机械导轨的方式给机器人定位。这样的方法不仅改造起来成本很大,维护成本也很大,同时对餐厅的整体装潢也有很大影响。采用视觉定位算法之后,就不需要任何导轨来辅助定位了。机器人有了真正能够使用的眼睛。同样工业上的AGV机器人也可以采用视觉定位的方式给机器人提供更精准的坐标。
更新:
经过长时间的测试开发,我们已经开发出一套稳定和完善的视觉导航系统。即伽利略视觉导航系统。更详细的信息可以看这里(http://www.bwbot.org/zh-hans/content/galileo)。伽利略系统相关文档介绍(https://galileo-servicebot-doc.bwbot.org/)
伽利略视觉导航系统是一个融合了多种传感器,以视觉导航为主导的机器人定位和运动控制系统。通过加载本系统可以实现机器人的定位和导航功能。适用于自动巡检机器人工业AGV,服务机器人等多种应用场景。
下面是一个操作视频,包含了创建地图和保存地图的操作。更详细的内容可以查看伽利略系统相关页面。
-
The visual navigation algorithm was first applied to the production environment.
2016.7.19
Recently received a robot order from the user. The user needs to make an exhibition robot and put it in his showroom. The entire exhibition hall is about 30 meters long, and the products of the user exhibition are arranged in turn on the side of the exhibition hall. Users need robots to stop at the products of each exhibition and introduce the product. At present, this user’s robot uses a tracking method, which puts a black route on the floor and indicates the first few products at that time. However, the user is very dissatisfied with these black lines and feels that the atmosphere of the entire exhibition hall is destroyed.This situation must use our visual positioning system. However, our visual positioning system is not yet mature, and the program can be accurately and stably operated. But since users have such a demand, they can only try it.
The video above is a visual display of visual navigation. It can be seen that the visual positioning is highly accurate and works very stable. The program sets the car to run in the same direction as the black line. No matter how humans interfere, the car can return to its original direction. This is not possible with inertial navigation using gyroscopes and encoders. Inertial Navigation Once the wheels slip, the positioning creates an unrepairable error.
Above is a broader test video. So far, Xiaoqiang’s visual navigation system has finally been used in the production environment.
-
视觉导航算法第一次应用于生产环境了
2016.7.19
最近接到了用户的一个机器人订单。用户需要做一个展览用机器人,放在他的展厅里面。整个展厅长大概有三十多米,用户展览的产品在展厅一侧依次排开。用户需要机器人在每个展览的产品处停下并介绍这个产品。目前这个用户的机器人采用的是循迹的方法,在地板上贴上黑色的路线,并在上面标明这时第几个产品。但是用户对这些黑线很不满意,觉得破坏了整个展厅的氛围。
这种情况就必须用到我们的视觉定位系统了。然而视觉我们的视觉定位系统尚未成熟,程序能否准确稳定的运行也没有把握。但是用户既然有这样的需求也就只能试试了。
上面的视频就是视觉导航的效果展示。可以看到视觉定位的精度很高,工作起来也非常稳定。程序设置小车按照和黑线一致的方向运行。无论人为如何干扰,小车都能回到原来的方向。这个是利用陀螺仪和编码器的惯性导航无法做到的。惯性导航一旦轮子发生打滑,定位就会产生无法修复的误差。
上面是一个范围更加广的测试视频。至此小强的视觉导航系统终于被用于生产环境了。
-
Intelligent robot storage management system case
2016.9.3
In the production process of the factory, it is often difficult to manage the materials. For example, due to the lack of timely preparation of materials, the production is delayed. Improper material management leads to unnecessary losses. There are no clear material records that result in unclear costing and so on. In order to solve these problems, we have developed a management system for a clothing company in Dongguan.
The main structure of the system is shown below:
Ou Meng material management system structure diagram
Material management personnel at the system plant can easily manage and count materials. The previous production process was further standardized and systemized to reduce the losses caused by improper operations. With this management system, the storage system can be truly converted into a logistics system for efficient and precise production.
Management system interface:
Management system hardware:
-
智能机器人仓储管理系统案例
2016.9.3
在工厂的生产过程中经常会为物料的管理而犯难。比如由于物料没有及时准备完全导致生产延期。物料管理不当导致产生不必要的损耗。没有明确的物料记录导致成本核算不清等等。为了解决这些问题我们专门给东莞一家服饰公司开发了一套管理系统。
系统的主要结构如下图所示:
欧梦物料管理系统结构图
通过这套系统工厂的物料管理人员可以方便的对物料进行管理和统计。也把之前的生产流程进一步规范化和系统化,减少由于不当操作带来的损失。采用这套管理系统后能够真正的把仓储系统转换成物流系统,实现高效和精确的生产。
管理系统界面:
管理系统硬件:
-
视觉巡检机器人发布
2016.10.1
巡检机器人就是像保安一样在特定场地巡逻的机器人。一般的巡检机器人只能通过远程遥控进行操作。采用视觉导航技术后,巡检机器人就可以自动的在设定好的路线上进行巡检,省去进行遥控和监测的人力。
视觉巡检机器人测试视频
上面的视频是利用视觉导航技术开发的巡检机器人。机器人按照软件设定的巡检路线进行移动。
视频中左侧是摄像头实时采集到的图像,右侧是在视觉地图中小车的实时位置显示。图像中的绿色点代表障碍物特征点。绿色的方块是小车的当前位置。红色的曲线是小车的目标巡检路线。可以看出巡检机器人能够稳定的沿着红色的曲线移动。软件的操作也是十分的方便。通过专门的软件创建地图之后,在地图上标记出想要巡检的具体路线。之后点击开始巡检按钮就可以开始自动巡检了。
-
Visual inspection robot released
2016.10.1
A patrol robot is a robot that patrols a specific site like a security guard. The general inspection robot can only be operated by remote control. After adopting the visual navigation technology, the inspection robot can automatically perform inspection on the set route, eliminating the manpower for remote control and monitoring.
Visual inspection robot test video
The above video is a patrol robot developed using visual navigation technology. The robot moves according to the inspection route set by the software.
The left side of the video is the image captured by the camera in real time, and the right side is the real-time position display of the car in the visual map. The green dots in the image represent obstacle feature points. The green square is the current location of the car. The red curve is the target inspection route for the car. It can be seen that the inspection robot can stably move along the red curve.The operation of the software is also very convenient. After creating a map with specialized software, mark the specific route you want to patrol on the map. Then click the Start Patrol button to start the automatic inspection.
-
Indoor delivery robot, red rabbit, debut
2016.10.18
After a long period of development, our indoor delivery robot Red Rabbit finally has to meet with you at the high-tech fair. Red rabbits use visual navigation technology. The image information collected by the camera is processed to return to the current position of the machine. With specially developed control software, users can easily set up the red rabbit delivery line. The red rabbit is easy to use and stable, and is very suitable for indoor delivery applications.
Red rabbit rendering
Red Rabbit Software Control Interface -
室内投递机器人赤兔登场
2016.10.18
经过长时间的开发,我们的室内投递机器人赤兔终于要在高交会和大家见面了。赤兔采用视觉导航技术。通过处理摄像头采集到的图像信息回去机器当前的位置。通过专门开发的控制软件,用户可以轻松的对赤兔的投递线路进行设置。赤兔使用方便运行稳定,非常适合于室内投递的应用场景。
赤兔效果图
赤兔软件控制界面 -
小强XQ-mini发布了
2017.3.21
备受大家欢迎的小强ROS开发平台迎来了自己的小兄弟,小强mini。
小强mini的尺寸更小,采用更低性能的处理器,适合于没有大量计算的使用场景。具体参数配置如下:
需要的客户请在网站点击购买。 -
Xiaoqiang mini released
2017.3.21
Xiaoqiang’s ROS development platform, which has been well received by everyone, ushered in its own little brother, Xiaoqiang mini.
The Xiaoqiang mini is smaller in size and uses a lower performance processor, which is suitable for use scenarios without a lot of calculations. The specific parameters are configured as follows:
Customers who need it, please click on the website to purchase. -
小强ROS机器人开发平台走出国门
2017.4.10
小强ROS平台终于走出国门走向世界了!小强为世界ROS开发者提供了中国的优秀开发平台,目前小强已经销往美国、新加坡、印度尼西亚、芬兰、阿联酋等国家,受到了消费者的喜爱,小强开发平台是中国最早的国产ROS开发平台,经过更新迭代,已经进化出了强大的功能。小强未来注定会更加强大!
曾经的初版小强是这样的:
现在是这样:
小强希望与您一同成长,未来的小强将会是怎样?您说的算!
-
Xiaoqiang ROS robot development platform goes abroad
2017.4.10
Xiaoqiang ROS platform has finally gone abroad to the world! Xiaoqiang has provided China’s excellent development platform for ROS developers. At present, Xiaoqiang has been sold to the United States, Singapore, Indonesia, Finland, United Arab Emirates and other countries, and has been loved by consumers. Xiaoqiang Development Platform is China’s first domestic ROS development platform. After the iteration of the update, powerful features have evolved. Xiaoqiang’s future is destined to be even stronger!
The first version of Xiaoqiang was like this:
This is now the case:
Xiaoqiang hopes to grow with you, what will be the future Xiaoqiang? What you said!